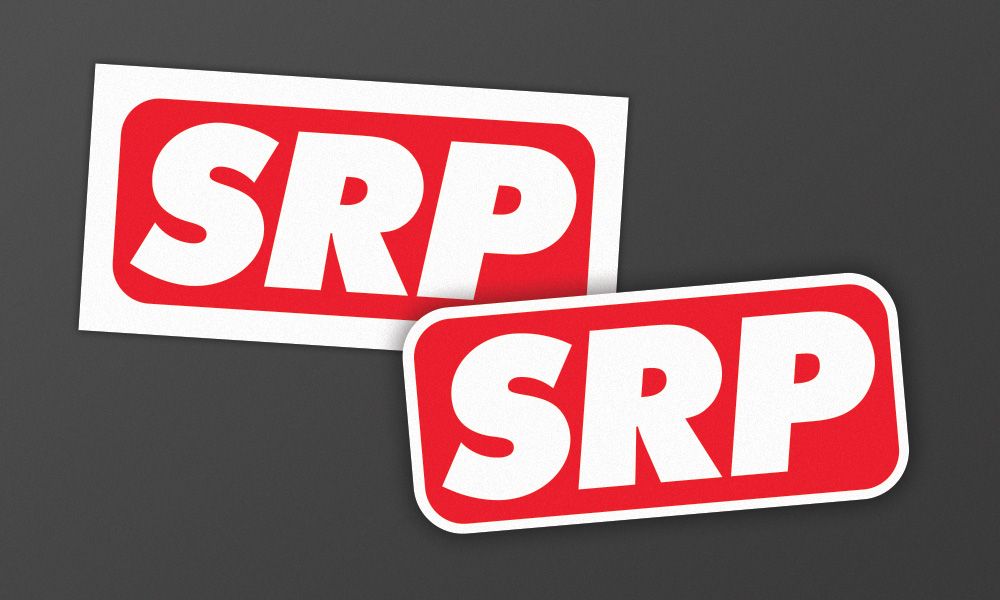
Kiss Cutting vs. Die Cutting for Custom Gaskets: Understanding the Pros and Cons
In the world of flexible material cutting, the choice between kiss cutting and die cutting can significantly how your custom gasket looks and functions.
Tolerance requirements, output and material considerations are all considerations in your custom gasket order, as we determine the most suitable method for machining custom parts from your chosen material.
In the following, we’ll walk you through the differences between kiss cutting and die cutting, along with considerations we use to choose the best machining method to manufacture your custom gasket order.
Kiss Cutting vs. Die Cutting: What’s the difference?
Die Cutting
Die cutting is a term that’s often used to describe machining custom shapes from a material. The most common method uses a sharp steel die to cut shapes from the layers of foil, film, foam and adhesive.
- Die cutting is a term that’s sometimes used interchangeably with through-cuts, which is when the die punctures through all layers of material, and meets the metal anvil.
- Flatbed die cutting is the most standard and oldest method for cutting identical shapes out of rolls and sheets of foam, tape and other flexible material.
- Much like a cookie cutter, the sharp-edged die or a steel rule is pressed directly into the material using a hydraulic press until it meets the metal anvil on the other side.
- After cutting, the part is completely separated from the remaining matrix, or waste material.
Further reading: Die-cutting for Custom Gaskets: Understanding the Pros and Cons
Kiss Cutting
Kiss cutting is one of several die-cutting methods, and it’s often used to create a roll or sheet of peel-and-stick gaskets on a release liner.
- Unlike a through-cut, the die does not pass through all layers of materials.
- The die is calibrated to end the cut just before reaching the very top layer of material that needs to remain uncut. For most kiss cutting products, the uncut material would be the release liner backing for the pressure sensitive adhesive. Once the cut is made, the matrix, or waste material, is cleared away, leaving the shapes on a liner.
- The most common machine method for kiss cutting is a rotary die press. But kiss cuts can also be achieved with a software-guided laser cutter, where the beam cuts down into the specified depth of the material.
Other considerations when choosing between die cutting and kiss cutting
There’s no one cutting method that suits every job. That’s why we plan production around what achieves the highest quality at the best value to you. Here are just some of the top considerations that factor into the decision of which machining method is best to produce your part.
Tolerance Requirements and Material Considerations
For parts that require precise measurements with little deviation, flatbed die cutting will achieve consistent output with sharper edges, as the cuts are performed straight into the material.
Rotary die cuts made with a cylindrical die are less suited for thicker foams and sponge materials, particularly for jobs with narrow tolerance requirements. In these instances, flatbed die cutting can provide an alternative that produces the results you’re looking for.
However, for thinner materials, rotary die cutting and laser cutting can yield tight tolerances.
Which Method Is Most Efficient?
Rotary die cutting can produce a higher output in less time than flatbed diet cutting, whether used to make kiss cuts or through cuts. (Rotary die cutting is capable of achieving both.) As the cylindrical die rolls over the material, it’s constantly producing shapes, making it ideal for high-volume jobs.
When used for making kiss cuts, rotary die cutting is a method that also makes assembly more efficient. When the gaskets and other types of adhesive-backed parts are presented on a release liner — whether on a sheet or a roll — the parts are easy to remove, easier to handle and require no sorting.
Flatbed die cutting, on the other hand, is more ideal for through cuts and kiss cutting thicker materials. It offers a rapid changeover, but the machining is slower than the rotary method as the hydraulic press stamps out one shape at a time.
When done well, kiss cutting is highly efficient and keeps material waste to a minimum. However, kiss cutting requires highly skilled machinists and ongoing monitoring for quality control and to make sure the die is achieving those precise cuts. Otherwise, cuts that are too shallow can ruin the parts on the liner.
Let SRP be your resource for custom gaskets
Whether you need a classic round gasket or an intricate cutout, SRP has the tools and skills to bring your project to completion. Fill out our online form for a fast, accurate quote.