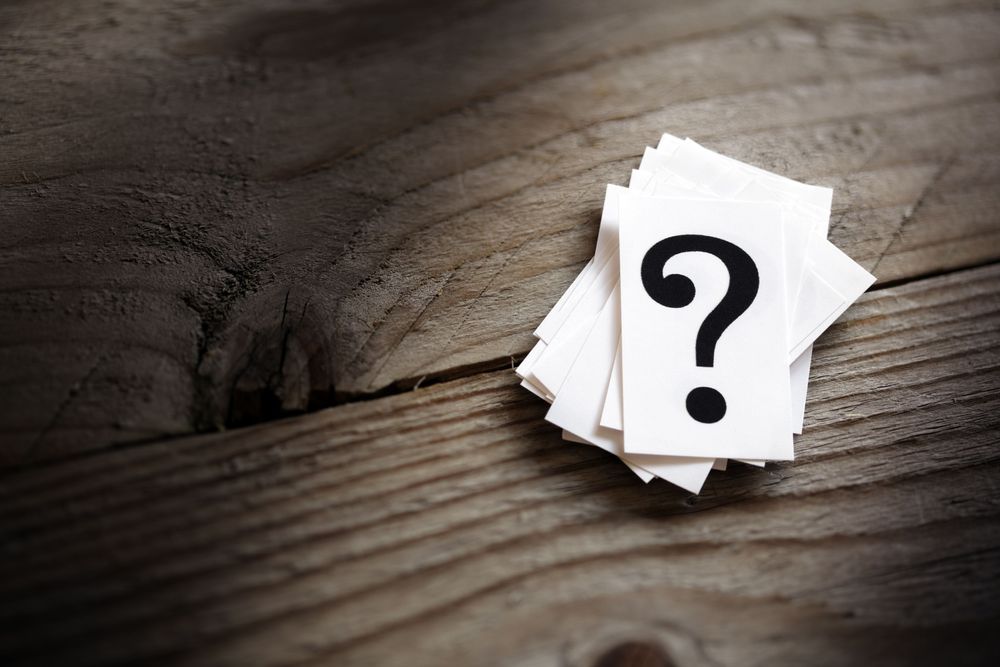
What to Know Before Your Gasket Design Consultation: 8 Key Questions
In gasket design, details matter. The more we know upfront, the faster and more accurately we can deliver the best-fit solution — on time and within budget.
Use this checklist to prepare for your consultation with SRP and ensure a smooth process from start to finish.
1. Do you have a CAD file?
This may seem like an elementary question to most customers. However, those who are new to product design may not realize the importance of this step until the time comes to unite the various pieces and parts of your product with custom die-cut gaskets.
Converting your gasket design to a CAD provides us with the best representation of the gasket’s visuals and dimensions. This information lets us identify the material cutting method that best fits your requirements, including tolerance range, deadlines and budget, so we can give you a fast and accurate quote.
Even if you’re still finalizing your design, sharing a preliminary CAD file helps us recommend the right cutting method and begin prototyping more efficiently.
2. What is the gasket’s acceptable tolerance range?
Many customers overlook the nuances of factoring the right tolerance range for elastomeric materials. But during the design and planning stage, you’ll want to account for the small variations in dimensions that occur in a material during die-cutting. These variations (tolerances) are often imperceptible to the naked eye.
Most gaskets function flawlessly within the standard tolerance range. But if your gasket requires a tighter-than-standard range to hold everything together, we’ll need to look at higher-precision cutting methods. But that can increase your production and material costs, making the effort to identify the ideal tolerance range worthwhile
Different materials behave differently during die-cutting. Softer foams may require wider tolerances than rigid elastomers — another reason we ask this early on.
Providing this detail early lets us choose the cutting method that’s best for your gasket.
3. What does your gasket do?
Successful gasket design considers the material’s ability to protect and hold through the demanding conditions the product would be exposed to. In most cases, there would be a specific set of specifications to follow, which consider things like:
- Temperature: What temperature range would the material be exposed to?
- Location: Is this an indoor or outdoor application?
- Resistance to UV rays, chemicals and solvents: What would the material be exposed to, and how much and how often?
- Flame resistance: Would the material require a particular flame rating?
- Gasket function: What will the gasket be sealing or protecting?
For example, if your gasket needs to seal against water in an outdoor application, EPDM or BISCO® silicone may be ideal.
If shock absorption or vibration damping is required, PORON® polyurethane or neoprene sponge may be more appropriate.
The more we know about the end product, the better we can assist you in the materials selection and manufacturing processes.
4. Any quality requirements for your gasket’s project approval?
Some customers require extra documentation or testing — such as First Article Inspection Reports (FAIR), Certificates of Conformance (CoC), or material traceability reports.
Letting us know in advance helps us build your order to meet those expectations.
5. Does your project require a prototype?
If you need a prototype, let us know of any requirements that will be a part of your review .For high-volume or high-performance applications, we often recommend a quick-turn prototype to test gasket fit, sealing performance or adhesion.
6. What is your lead time?
At SRP, we build custom gaskets to order. We keep materials in stock, but we don’t maintain a warehouse of finished products. We typically quote 4–6 weeks, but many gasket orders ship within 3–4 weeks. If your project is on a fast track, let us know — we’ll do our best to expedite depending on material availability and workload. All orders are made in the U.S. in our Illinois facility.
7. What are your packaging requirements?
Packaging requirements can run the gamut in the gasket business. It’s an often-overlooked question that can affect the gasket delivery, especially if you’re looking for something specialized. Will you need a barcode for inventory management purposes? Will the gaskets need to be packaged in plastic zip-close bags, or would bulk packaging suffice?
Whether you need parts on a roll, individually bagged, or labeled for inventory management, we can customize the packaging to your workflow.
8. Are you prioritizing gasket makers within the Preferred Converter network?
When you’re looking to use specific gasket materials and adhesives for your project, you may have noticed that SRP is a part of the Preferred Converter network with several material providers, including 3M™. What does a preferred partnership mean to you? There are several benefits, which makes it an important feature to look for when you’re looking at gasket partners.
Being in the Preferred Converter network gives you access to the best materials in the industry. This is a point of pride for us because we know our customers can count on getting the highest quality materials at the highest standards. Not only that but being in the Preferred Converter network means we get the best available prices and lead times for the materials you need.
SRP is a 3M™ Preferred Converter and a trusted partner for other top-tier material brands. Here’s what that means for you:
- Access to industry-leading materials
- Faster lead times on in-demand substrates
- Cost advantages through trusted supplier relationships
- Confidence in consistent, high-quality production
In short, the Preferred Converter label is a signal to you that a company can provide top-notch materials and service.
Let SRP be your resource for custom gaskets
Ready to get started? Fill out our online form for a fast, accurate quote.